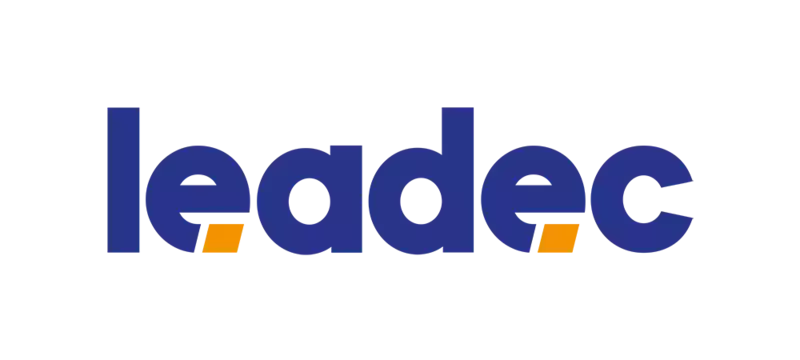
Objective
- Customer demands transparency through tracking
- Small time window for implementation
- Reduce delivery errors
Solution
- ZetesChronos, proof of delivery solution
Result
- Agile implementation within 3 weeks
- Documentation of all orders (POD)
- Drivers reliably guided through the process
- Customer sees actual delivery progress
- Almost zero error rate for maximum customer satisfaction
- Simplified invoice checking
Leadec is the global leading specialist in services along the entire life cycle of factories and associated infrastructure. With headquarters in Stuttgart, the company has approximately 18,000 employees worldwide. For nearly 60 years, Leadec has been supporting its customers along the entire production value chain. The service provider is present in more than 300 locations, often directly in the plants of its customers. For this project, they needed to have real-time visibility on their delivery process to allow the collaboration with a big German automotive company based in Bremen.
Extensive factory site
Leadec took over the supply of spare parts and consumables to the production facility. This ‘non-production material’ (NPM) is located in dedicated warehouses across the extensive factory site in Bremen to be called up on demand by numerous departments. The NPM consists of all materials that are not direct components of the end product but are essential for continuous production operation. The range extends from work gloves and tools to welding robots, altogether around 50.000 items. “If these things are missing, production comes to a stop – and that’s costly”, says Alexander Bölken, head of logistics at Leadec’s Bremen location.
Along with accurate on-time delivery, Leadec’s customer demands maximum transparency of open and closed processes. They want real-time visibility for the whole delivery process, as well as the times and places of goods transfer. They also want monthly billing to be easily comprehensible and controllable based on a digital record of services.
Real-time transparency
At the start of the tender phase, Leadec surveyed potential solutions so that they could respond quickly. The company learned about ZetesChronos electronic proof-of-delivery software for controlling and optimising pick-up, delivery and management processes. The solution links drivers, back office employees and logistics management to provide real-time transparency for goods, vehicles and returnable assets. It enables management to give them continuous insight into the status of their orders.
“We were convinced by ZetesChronos and by Zetes’ reputation as a supply chain technology company”, reports Bölken. When the logistics contract was officially confirmed in October, Zetes also got the order. “After that we had only three weeks to the go-live.”, adds Bölken.
Intuition instead of a manual
The test system, which allows new processes to be tested safely using real data, proved to be very helpful during the short project period. "We were able to test the solution in advance on the test platform, and we found it to be extremely intuitive and easy to use. After that we no longer needed a manual”, confirms Bölken.
The key elements of the solution include the proof-of-delivery app and a cloud based management visibility platform incorporating multiple various dashboards for capturing, planning, monitoring and analysing deliveries. Based on this, two planners generate loading lists out of the system for the delivery vehicles. Each truck makes up to three trips per day, carrying 50 to 70 returnable containers and pallets, as well as around 120 to 200 parcels, from the NPM warehouses to the individual departments. Seamless documentation of the transport operations is essential, in part due to the high value of the goods.
The delivery process begins with sending the trip data to the mobile scanners of the drivers. These are sturdy Android hand-held devices in smartphone format. The display guides the driver through all orders and procedures. Loading errors are immediately noticeable because each shipment is first scanned and compared to the planning data by ZetesChronos. Discrepancies are signalled to the driver both audibly and visually.
Correct placement
When unloading, the barcode of the delivery point is scanned. There is also a photo function: the driver must photograph the unloaded pallets or containers to document correct delivery. The photos also serve as a delivery receipt and can be retrieved by the customer via the ZetesChronos online platform, the same as all other delivery data and times. “Every standard order must be delivered within 24 hours”, explains Bölken. For urgent spare parts there is an express delivery service, which takes only 45 minutes on a special route.
Short communication paths
Integration of parcel deliveries in ZetesChronos is one of the project steps that was implemented without haste after the on-time start, along with the previously made changes to the reports. “Our customer has very clear ideas about how we document our services. For this Zetes has created specific reports for us”, says Bölken, who is very satisfied with the cooperation with Zetes. “Zetes Customer Service always responds very quickly and constructively to our change requests”, notes the department manager, adding that communication is marked by “short paths and quick agreements.”
“The processes and control mechanisms defined by the system result in an extremely low error rate, leading to very high customer satisfaction.” Alexander Bölken, head of logistics at Leadec’s Bremen location
Leadec sees a positive balance after the first four months. ZetesChronos has been running stably and reliably. The processes and control mechanisms defined by the system result in an extremely low error rate, leading to very high customer satisfaction. Of the approximately 15,000 shipments transported up to now, there were only ten incorrect deliveries, corresponding to an error rate of less than 0.067 per cent. Each of these cases was investigated in detail, allowing Bölken to confidently forecast: “We can also achieve a zero error rate.”
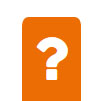
