
OBJECTIVES
- Comply with the new requirements for medicine traceability
- Maintain existing productivity levels
- Ensure very short delivery lead times
SOLUTION
- ZetesMedea Voice powered by MCL Voice
- Multimodal, multi-customer voice picking
- Motorola WT4090 terminal
- Motorola RS507 ring scanner
- Headsets for voice terminals
RESULTS
- Greater working efficiency for 1,000 operators in 40 locations
- Less than 0.07% picking errors
- Full traceability of medicines
- Reduced number of stages required for preparation and inventory
- Permanent reliable inventory maintained
The wholesaler distributor CERP Rouen (Astera Cooperative Group) has reorganised its order picking and permanent inventory logistics processes to comply with new medicine traceability standards, without compromising the productivity required to ensure very short delivery times. Medicine traceability is fully guaranteed using the ZetesMedea logistics execution solution with its multimodal capability combining voice and product scanning.
Around forty sites have been deployed in France and Belgium, which means almost one thousand operators are working with the solution. Other business processes like product stocking and locating, will soon be optimised with the same solution.
Picking and delivering medicines in two hours CERP Rouen is a subsidiary of the Astera Cooperative Group, a specialist in pharmaceutical distribution. The wholesalerdispatcher distributes products from 32 agencies and three warehouses in France and four agencies in Belgium. Around 30,000 items are delivered to 6,500 pharmacies up to three times a day within an average time of two hours from receipt of order.
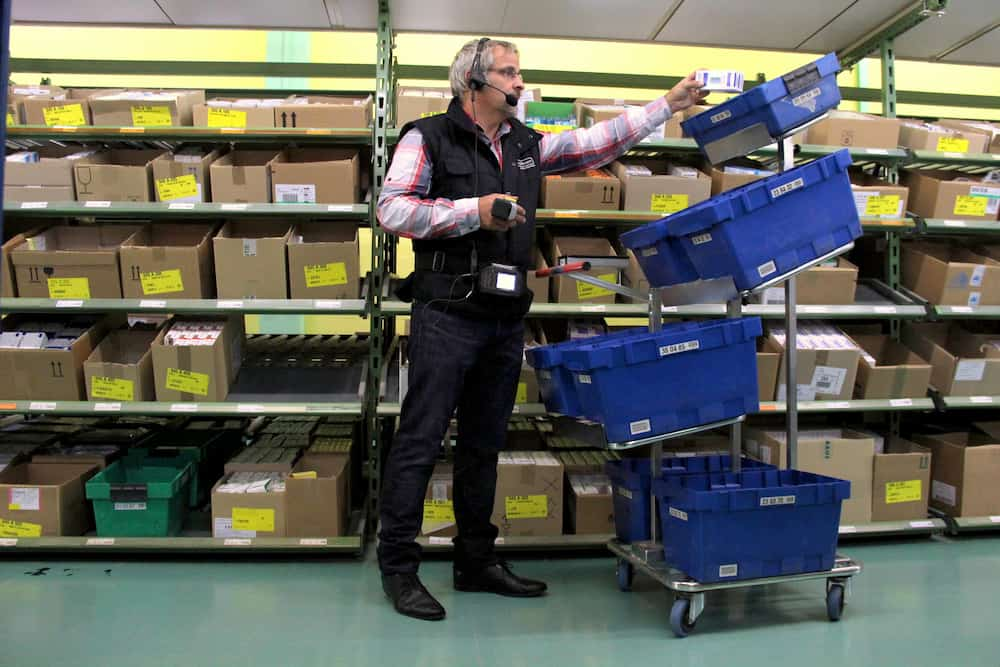
Towards 100% traceability
In 2008, the company installed two 2D readers to deal with veterinary items marked with the Datamatrix code and to optimise the receipt and storage of medicines on a FIFO/FEFO basis. This reorganisation of logistics processes was prompted by a number of factors: the introduction of Datamatrix codes; mandatory medicine traceability standards introduced to the pharmaceutical sector in 2011; and an increasing number of items with compliant markings.
Until then, with the exception of a few automated sites in Belgium where voice picking had been introduced for order preparation, inventory and picking processes were paper-based. Products were checked visually and traceability remained sketchy.
2D barcode scanning, voice or both?
Two companies were contacted to submit a solution based on 2D data capture. The aim: to establish a system capable of complying with new traceability regulations, without penalising the high productivity levels that ensure the very short delivery times guaranteed by the company. It was envisaged that several systems would be required to enable total traceability - scanning with mobile 2D readers and voice. A pilot project was set up in 2010 on a test site at Conflans-Sainte-Honorine and
the ZetesMedea warehouse process optimisation solution was selected as the preferred option.
“With a single investment and the same equipment, we can optimise several business processes such as preparation and inventory, but also warehousing and product placement.”
Anne Claude Mare, Head of Development and Business Research at CERP Rouen
ZetesMedea is a logistics execution system that efficiently drives all warehouse processes. Its goal is to organise processes quickly and flexibly whilst removing errors and reducing costs. The solution’s voice module, ZetesMedea Voice, offers a multimodal approach that combines voice and 1D or 2D scanning.
Anne-Claude Mare, Head of Development and Business Research at CERP Rouen said: “We agreed on the scanning part right from the start, but had reservations about the installation of the voice system with possible resistance from operators. After this test and the initial very positive feedback from users, we emphasised this at our Belgian site at Courcelles and two other French sites at Verneuil and Agen during 2011”.
The ability to upgrade was another significant advantage in choosing Zetes as a supplier. With possible changes to European regulations on the traceability of pharmaceutical products, a serial number check could ultimately be introduced. A few small adjustments to ZetesMedea would give CERP Rouen the option of extending its controls to a few targeted ranges and put this into practice easily with ZetesMedea Voice.
Optimising multiple processes with the same solution
Multimodal, multi-customer voice picking
CERP Rouen has to deal with two large waves of orders - one between 11.30 a.m. and 1 p.m. and the second between 6.30 p.m. and 8.30 p.m. and sometimes up to 10 p.m. for certain pharmacies in major urban areas. These two waves of orders are then delivered from 2 p.m. onwards and into the following morning. A third, smaller delivery can sometimes be made towards 4 p.m. on the same day.
Anne-Claude Mare, Head of Development and Business Research at CERP Rouen: “Until recent years, with no traceability obligations, we were able to manage distribution performance without the assistance of ZetesMedea, but this has become increasingly difficult as the number of traceable items has grown, mainly on non automated sites”. Depending on the size of agency, orders are picked on conveyor belts (for the largest sites) or specific multi-tray/multi-customer trolleys.
CERP’s Rouen operators working with ZetesMedea Voice are equipped with a mobile terminal (Motorola WT4090), a ring scanner (Motorola RS507), plus headset. The voice system guides the operator through the process, telling him which products to pick, the quantity, location and final destination point, just as in traditional voice order picking. In addition, the system also advises which elements must be scanned to ensure traceability: the detachable label (containing price information) and/or the Datamatrix (containing batch number and expiry date information) and/or the barcode identifying the product and/or the location code. The system immediately corrects any errors made by the operator, for example picking an incorrect product or quantity. If further assistance is needed, the operator is able to ask a question of the system out loud, or consult information on the mobile terminal screen.
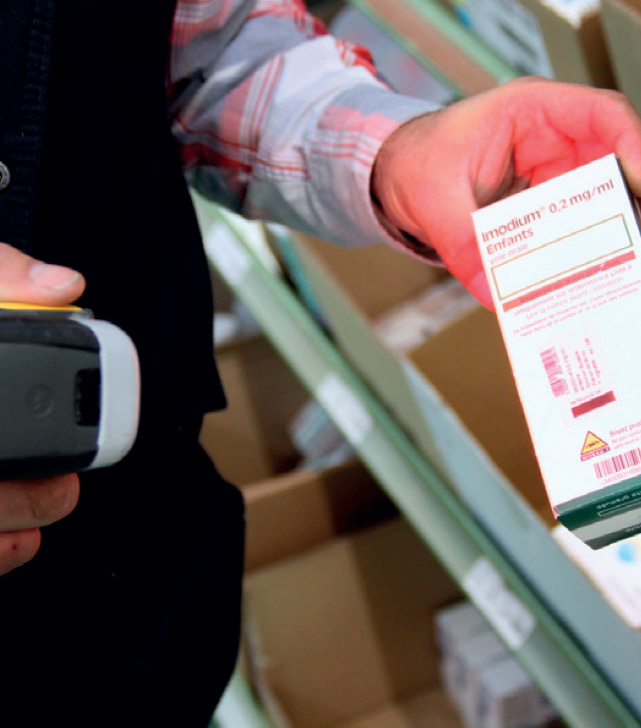
Permanent reliable inventory
Similar processes apply for the daily inventory. Using the same equipment, the operator is guided by the system throughout the permanent inventory process. The solution has simplified tasks considerably: enabling paperless operation, safety of traceability data capture via scanning, registration of quantities counted and real time stock updates.
Untrained voice system powered by MCL Voice
Powered by the MCL Voice speech platform, the ZetesMedea Voice system is an ‘untrained’ system, which means that the operators do not need either prepared training or to register a voice profile. They can start working straight away. The solution has also been fully integrated with the company’s pre-existing WMS (warehouse management system).
Advantages
Working more efficiently
The operators work more efficiently given the greater convenience and freeing up of eyes and hands (no more paper dockets and pencils). The installation of voice picking has also eliminated certain preparation or inventory stages. For example, operators no longer need to control either the item, batch code or the price on the detachable label, as the system does it automatically by scanning the barcode or Datamatrix. CERP Rouen can also manage certain aspects of the preparation process more easily using the solution. For example, if a product is no longer available on the shelf, the operator simply has to say “stock” into his headphones, without moving from his position, to find out how many units remain in general stock. Before introducing ZetesMedea Voice, this information could only be obtained on one of the site’s computers. In addition, when an operator needs to pick or count a large number of units, the voice solution can specify what is still needed to be picked or counted. This feature helps to limit errors made due to the size of the order or levels of stock to be counted.
Maximum traceability and operating gains
Today, product scanning is an efficient check that provides full traceability. CERP Rouen has improved productivity levels due to the efficiency of the system, whilst keeping levels of disruption for users to a minimum. Picking errors have also been reduced to less than 0.07%.
Thus, whilst meeting requirements for regulatory traceability, the solution chosen has matched all agency types (large and small, conveyor belt and trolley preparation method) and CERP Rouen has managed to maintain a consistent level of efficiency and customer satisfaction across all its sites.
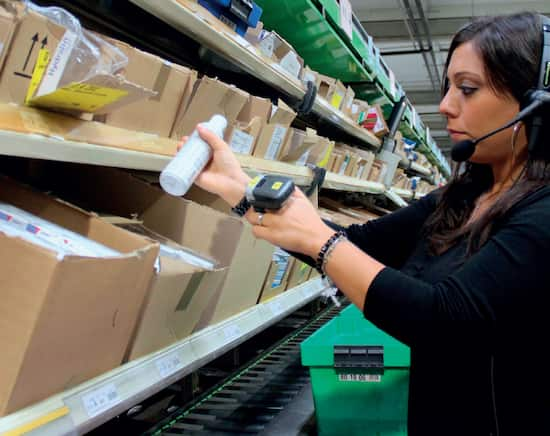
“Our requirements were very high, especially in terms of response times and system efficiency; Zetes has met our expectations perfectly by adapting the solution to meet our needs.”
Anne Claude Mare, Head of Development and Business Research at CERP Rouen
Versatility of the solution and return on investment
More than one thousand operators are now equipped with the same solution and hardware. This has a financial advantage as well as lowering workloads: “In addition to improving traceability, quality and productivity, several business processes can be optimised with a single investment, for example picking and inventory, plus product re-stocking and locating, which we plan to introduce in the future”, says Anne-Claude Mare.